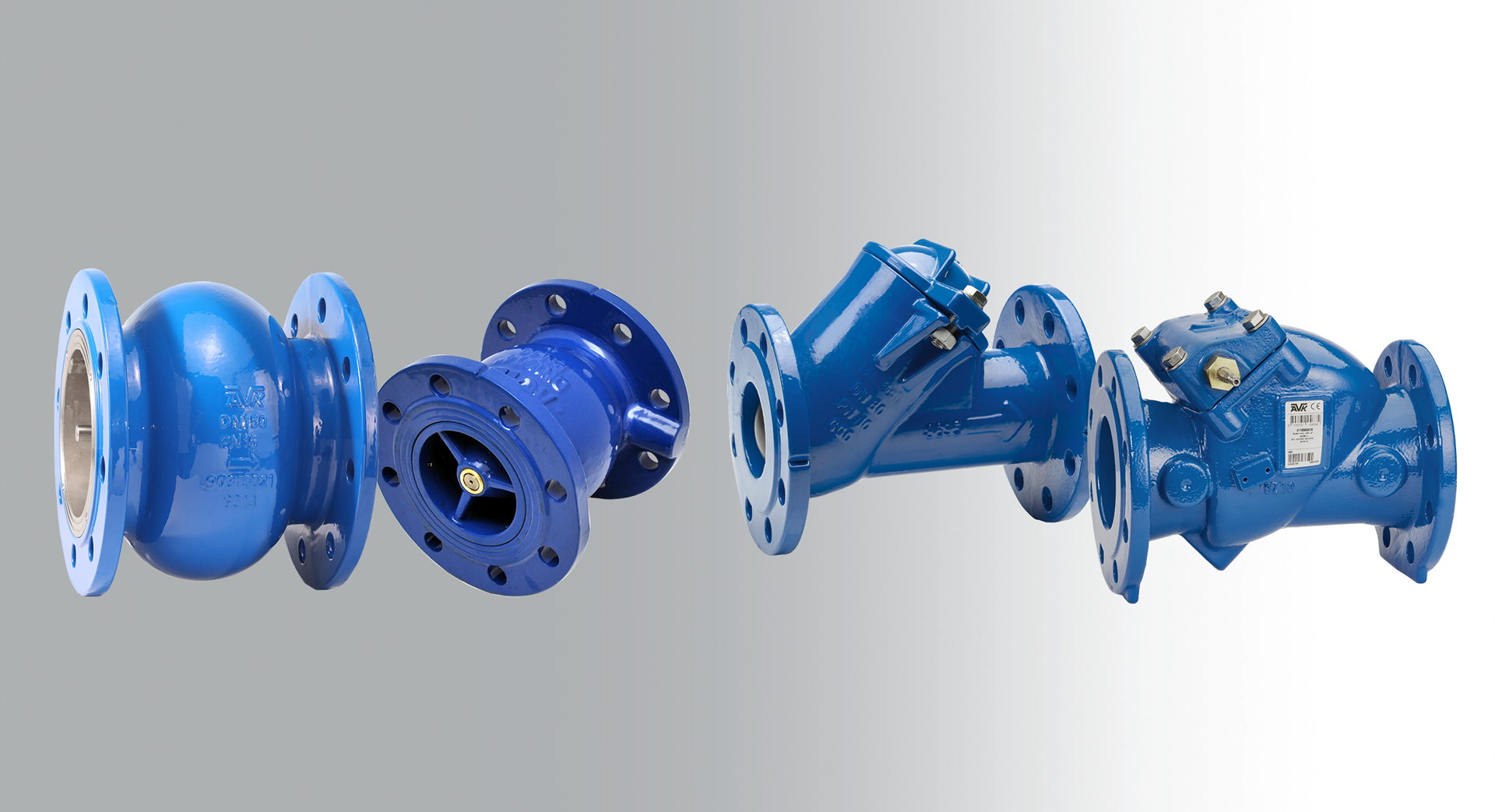
How to select the right check valve
First of all, there is not one type of check valve being the best choice for all applications and the selection criteria may not be equally important for all cases. The importance of selecting the correct type, size and specification of check valve is crucial to ensure the running of the system is smooth, trouble free and provides long‐term operation.
Swing check valves
Swing check valves are the most common check valves. They are inexpensive and as they are automatic they do not require any external power or control to operate – only the flow direction determines the valve operation. Swing check valves with closed bushings do not have an open/close indicator but often the valves are mounted with lever and weight or lever and spring which enable visual check. For more details, please visit the section about swing check valves.
Ball check valves
In general, ball check valves are simple and cost effective. Advantages are their compactness and the fact that they have no external parts which helps keeping the price low and the reliability high. A disadvantage may for some applications be that they do not have an open/close indicator. For more details, please visit the section about ball check valves.
Recoil check valve
The recoil check valve is one of the oldest and recognized types of high performance check valves. They are used in pumping systems where high rapid flow reversal takes place. Typically, these active systems are pumping stations which adopt high branch velocities and, in addition, provide automatic stopping and starting, deliver into a vertically rising main and have multi‐pump sets delivering into a common main.
The recoil check valve is designed to incorporate every mechanical and hydraulic assistance for accelerating the closure of the door.
- Mechanical assistance is given by a combination of inertia reduction, concentration of mass and ideal suspension of the moving elements.
- Hydraulic assistance is given by the provision for forward and backward water streams within the body and around the valve door
For larger valve sizes, a multi‐door design is used. By sharing the volume of flow by two, three or even four doors, this reduces the required angular travel of each door, thus reducing the closure times of the doors.
The recoil check valves have metal to metal seats and an allowable leakage rate is to be considered.
Selection and sizing of check valve
There are a number of different types of check valves available for water and waste water systems. Where a check valve is required, it is crucial that the correct type and size is selected so that the system will:
- Operate smoothly with optimised efficiency
- Have reduced levels of maintenance, repair and shutdown
- Have an increased lifetime
The following points should always be considered when selecting check valves:
Fluid media
- For waste water, it is important that the valve has a full, clear bore design to allow solids to pass.
Flow rates (minimum and maximum)
- This allows the correct valve size to be calculated. Different check valve types reach the fully open position at different flow velocities.
- To optimise system efficiency, it is important that the valve will be in the fully open position under normal flow conditions as this will minimise the head loss across the valve. It also ensures that wear and tear on the internal moving parts are minimised and that it will operate under stable conditions.
- The maximum flow velocity is generally governed by relevant international standards (such as BS EN1074‐1) and 4m/s considered the maximum.
Working pressure at inlet and outlet (minimum and maximum)
- This will determine the pressure rating of the valve (e.g. PN10, 16, 25 etc)
- It is important to know the cracking pressure of the valve as this is the inlet pressure that flow begins to pass through the valve.
- The reseal pressure (downstream side of disc) is that which provides sufficient force to the disc to affect a seal and is especially important in low pressure systems.
- Energy consumption costs are higher for valves with increased head loss.
Headloss
Headloss is a function of fluid velocity and the valve headloss is affected by the flow conditions of the system and the internal surface of the valve. The geometry of the valve body and the closure design determines the flow area through the valve and thereby also affects the headloss.
The headloss to be considered is a combination of static head (caused by elevation difference) and friction head (caused by the internal of the pipes and valves). There are a number of formulas for headloss and rating of valves based on this. The most common is probably the flow coefficient of the amount of water passing through the valve at a certain pressure drop during a certain amount of time. However, for comparisons the resistance coefficient Kv is considered the best choice.
Total cost of ownership
The costs for your check valve may consist of more than just the purchase price. For some installations, the most important costs may be purchasing and installation but in other cases maintenance or energy costs may be equally or even more important. When considering costs as a selection criteria for your check valve, the total costs over the life of the valve should therefore be considered. In general, the more simple the valve construction is, the lower are the maintenance requirements.
Non-slam characteristics
Check valve slam results in system pressure surge. First step of the process is when the pumps stop and the flow is reversed. That may cause some reverse flow through the valve before it gets to a fully closed position. Then the reverse flow is shut off and the change in flow velocity turns the kinetic energy of the fluid into pressure.
A slam sounds like if the disc or the ball from the check valve is hitting the seat and can make quite some noise. However, the sound is not caused by the physical closing but by a sound wave arising from a pressure spike stretching the pipe wall. To completely avoid slamming, the check valve should close before any reverse velocity can occur. Unfortunately, that does not happen. The geometry of the valve decides how much reverse flow will occur so the faster the valve closes, the less slamming.
As swing check valves have the disc in the flow stream helping with rapid closure, they have better non-slam characteristics but today most pumps are frequency converted enabling them to adjust the start-up and closure time in order to avoid water hammer.
Check valves can be installed both horizontally and vertically. Slamming may be a bigger issue for vertical installations since a vertical flow reverses more rapidly but a vertical installation allows gravity to assist in closing the valve rapidly.