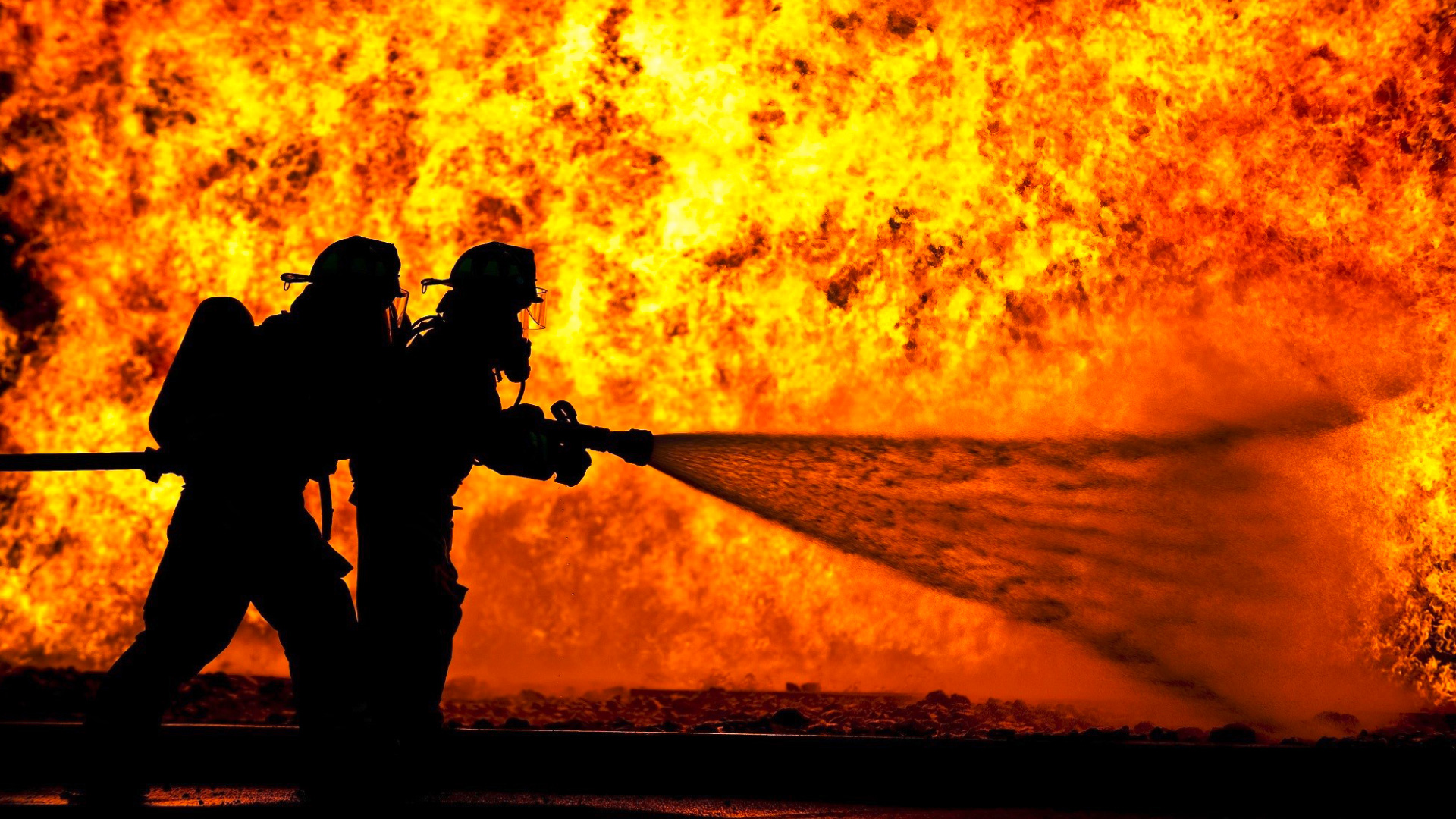
Safety approvals and property loss prevention
Product standards and approvals are ensuring quality, global recognition, safety and standardization. Approvals and listings are often required by the market and a listed mark shows the customer that the product has been tested according to some minimum requirements for its category. In addition, it shows that the supplier has committed to regular tests and audits as being performed by the approval organisation.
The UL and FM approvals are some of the most well recognized global standards and being able to mark our products with these adds great value.
UL standards, FM approval and AVK products
Since we always aim at the highest quality, most of our products for fire protection applications are approved according to both UL and FM. We have thus committed to meet the standards and requirements set by these well-recognized global organisations and to continuously test and control our product ranges accordingly.
Our UL listed and FM approved products count dry and wet barrel hydrants, butterfly valves, NRS gate valves, OS&Y gate valves, post indicators, wall post indicators and swing check valves.
You can read more about the specific approvals for each product series below.
FM Approval
FM Global is a property insurance company operating from the philosophy that most losses can be prevented. They provide insurance products and property loss prevention engineering services to protect their clients' worldwide operations.
FM Approval is part of the FM Global Group and it is a testing and certification service. Products that pass the five-step approval process are issued the globally acknowledged FM mark to support property loss prevention and to signify that they will perform as expected.
UL standards
Underwriters Laboratories (UL) is a product safety testing and certification company having developed more than 1,600 standards. UL is certifying, validating, testing, verifying, inspecting, auditing, advising and educating customers in 100+ countries.
In order to become UL Listed, a representative sample of the product to be listed must be tested and meet the safety requirements set. Products having the UL mark are covered by the Underwriters Laboratories follow-up program, which continuously tests the products to ensure that the UL standards and requirements are always met.
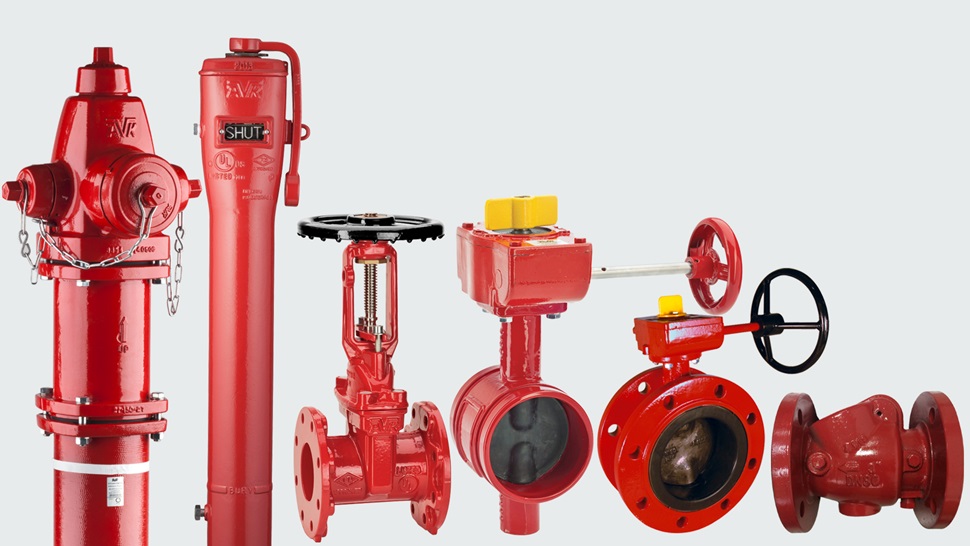
Testing and approval details for our FM and UL marked products
AVK wet barrel fire hydrants series 24 - according to FM 1511 and UL 246
The UL 246 standard for hydrants for fire protection service:
These requirements cover the performance of and methods for testing hydrants intended for use in piping systems supplying water for fire protection service.
The UL 246 approval tests include a 10-day moist ammonia air stress cracking test, testing of rubber parts according to UL 157 and tests of operation, leakage and head loss.
FM class number 1511:
Shell strength is tested by a pressure of four times the working pressure lasting for five minutes, and after the test there should be no evidence of damage. The standard also includes testing seat leakage at two times working pressure for five minutes without damage or leakage to be seen.
Furthermore, hose outlet strength, stem strength and head loss are tested.
AVK dry barrel fire hydrants series 27 - according to FM 1510 and UL 246
The UL 246 standard for hydrants for fire protection service:
These requirements cover the performance of and methods for testing hydrants intended for use in piping systems supplying water for fire protection service.
The UL 246 approval tests include a 10-day moist ammonia air stress cracking test, testing of rubber parts according to UL 157 and tests of operation, leakage and head loss.
FM class number 1510:
Shell strength is tested by a pressure of four times the working pressure lasting for five minutes, and after the test there should be no evidence of damage. The standard also includes testing seat leakage at two times working pressure for five minutes without damage or leakage to be seen.
Furthermore, hose outlet strength, stem strength and head loss are tested, and finally, the breakable system is tested by a pressurized hydrant (at maximum working pressure) being hit with a force sufficient enough to break. After separation, the hydrant must have a leakage of maximum 19 dm³/min while pressure is maintained for two minutes.
AVK post indicators series 34 - according to FM 1110 and UL 789
UL 789 standard for indicator post for fire protection service:
These requirements cover indicator posts, including wall and underground types, for use in operating valves of the inside-screw pattern and for indicating the position of the gates in such valves. Indicator posts are primarily intended for use with valves controlling water supplies to sprinkler, deluge, water spray, foam, and standpipe systems used in private fire service where connections enter buildings.
The UL 789 standard includes test of rotating and moving target mechanisms of position indicators and performance tests involving a 1,000 cycle operation test of polymeric parts.
FM class number 1110:
Visibility of the indicator is tested on a 12 meter distance and by simulating a heavy rainstorm it is waterproof tested to make sure that there is no collection of water inside.
A vertical indicator post should withstand 1220 Nm in both directions (for valves up to 350mm) – the value is 815 Nm for a wall type indicator post (up to 250mm).
Finally, non-metallic components are tested for resistance to temperatures as high as 427°C for two hours. After being cooled down again, the indicator post should be capable of full operation.
AVK gate valves series 45 - according to FM 1120-1130 and UL 262
UL 262 standard for gate valves for fire protection service:
These requirements cover gate valves intended for installation in piping systems supplying water for fire protection service.
The UL 262 standard includes a 10-day moist ammonia air stress cracking test, test of rubber parts according to UL 157, test of coating for seating surfaces and corrosion test for stems.
FM class number 1120 and 1130:
The valve body, cover and bonnet are subjected to a hydrostatic test of four times working pressure (or at least 48 bar) for five minutes and there should be no sustaining cracking or permanent distortion.
Stem seal leakage is tested on a partially open valve subjected to working pressure for five minutes. No visible stem leakage must appear. Both resilient and metal seats are also leakage tested.
Furthermore, rubber parts are tested for water absorption, corrosion protection coating, aging and bonding adequacy and the strength of gate, stem seal, indicator post and handle are tested.
AVK butterfly valves series 75 (indicating valves) - according to FM 1112
Disc strength is tested at two times working pressure held for five minutes and repeated for both directions. Hydrostatic strength is tested at a hydrostatic pressure of four times working pressure (or at least 48 bar) for five minutes. No visible rupture, cracking or permanent distortion of the valve body must be seen.
Seat leakage is tested at working pressure and at 125% of working pressure for five minutes each.
If there is any leakage, this should be compared to the allowed limits based on the seat type. The stem seal leakage is tested at working pressure in partially open position for five minutes, and cycling the disc six times during this time span, with no visible stem leakage allowed.
Furthermore, the FM standard also dictates tests of valve assembly strength, ultimate operator torque, durability, close quarters durability (butterfly type), friction loss determination, water hammer, indicator strength, water absorption, aging, corrosion protection coating and much more.
AVK gate valves series 145 - according to FM 1120-1130 and UL 262
UL 262 standard for gate valves for fire protection service:
These requirements cover gate valves intended for installation in piping systems supplying water for fire protection service.
The UL 262 standard includes a 10-day moist ammonia air stress cracking test, test of rubber parts according to UL 157, test of coating for seating surfaces and corrosion test for stems.
FM class number 1120 and 1130:
The valve body, cover and bonnet are subjected to a hydrostatic test of four times working pressure (or at least 48 bar) for five minutes and there should be no sustaining cracking or permanent distortion.
Stem seal leakage is tested on a partially open valve subjected to working pressure for five minutes. No visible stem leakage must appear. Both resilient and metal seats are also leakage tested.
Furthermore, rubber parts are tested for water absorption, corrosion protection coating, aging and bonding adequacy and the strength of gate, stem seal, indicator post and handle are tested.
AVK check valves series 5190 - according to FM 1210 (selected products) and UL 312
AVK series 5190 products for fire protection meet the UL 312 standard. The products 5190/10-001 and 5190/20-001 are furthermore approved according to the FM 1210 standard.
UL 312 Standard for check valves for fire protection service:
These requirements cover check valves DN25 and larger, used in piping systems supplying water for fire protection service. The UL 312 approval tests include a cycling performance test, testing of rubber parts, adhesion test for resilient seat materials and leakage test.
FM class number 1210:
The valve is subject to a cycle test of 50,000 cycles, no more than six cycles per minute. The test is carried out at atmospheric pressure and no excessive wear, damage or failure of any valve component must occur. Seat leakage tests are performed on resilient seat and metal-to-metal seats. For the resilient seat, no leakage is allowed during test with hydrostatic pressure of 2, 6.8 and 12 bar (and working pressure if higher than 12 bar) for five minutes each.
For the metal-to-metal seat, leakage must not exceed a value of approximately 11.8 ml/hour per centimeter of nominal valve size when subjected to 2, 6.8 and 12 bar (and working pressure if higher than 12 bar) for five minutes each.
In addition, clapper strength, hydrostatic strength, friction loss determination, bonding adequacy, water absorption and aging are also tested according to FM 1210 standards.