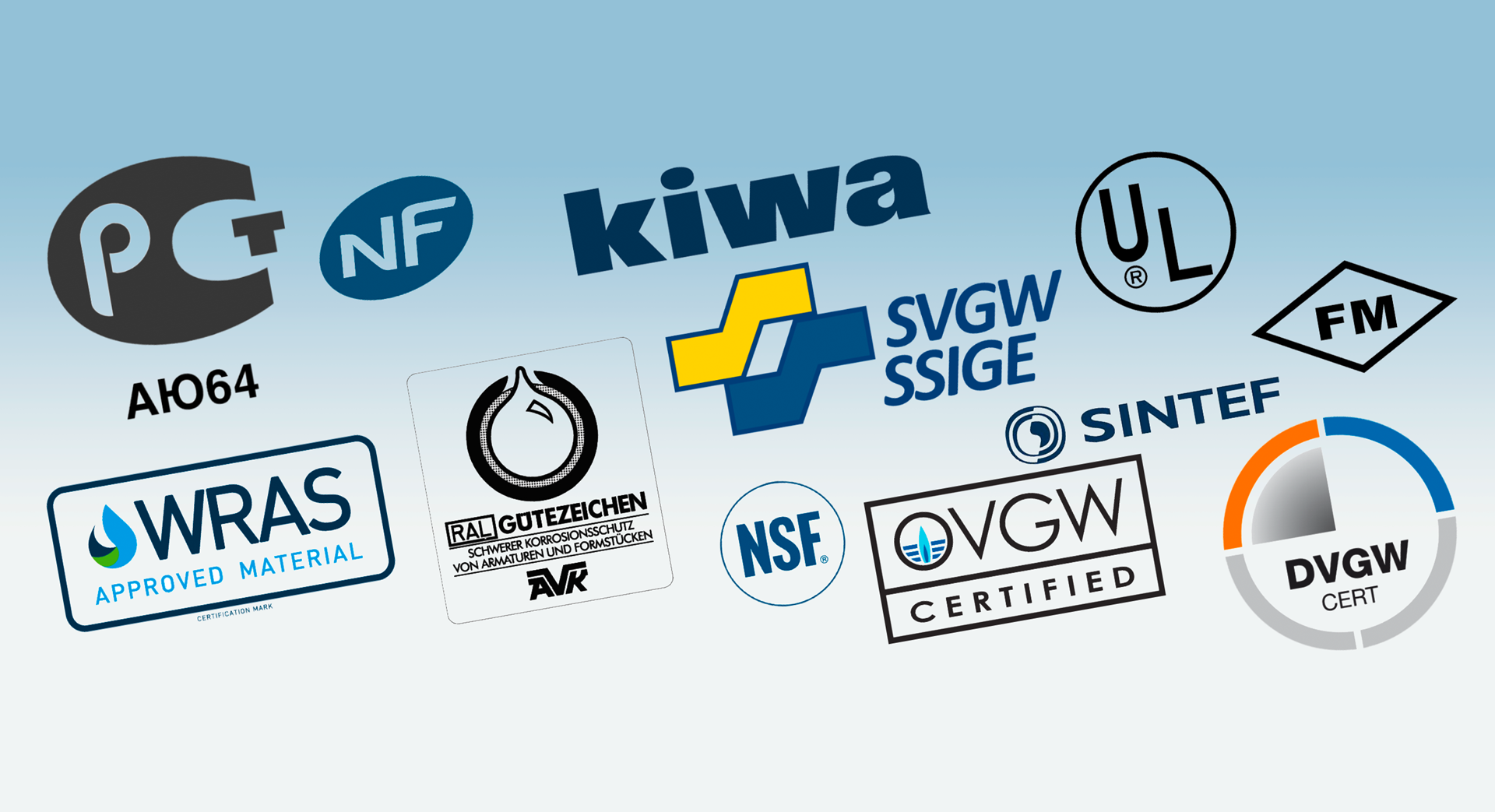
Investing in AVK valves is a commitment to safe drinking water
The quality and safety must be documented. This is where third party approvals comes in, by establishing a range of requirements regarding valve components and complete valves.
These approvals are especially important for drinking water applications, where it is important that materials do not present a risk of contamination, without affecting taste and smell.
Some of these approvals specifically refer to the materials such as rubber, epoxy coating, plastics and brass used in valves, and some with the complete valve and function. Surprisingly, there are very few pan-European standards. Instead, standards are determined at national level and even in some cases by the local water works in the respective countries.
Proof of quality and safety
Niels Jørgen Hedegaard, Head of Quality at AVK International A/S in Denmark adds: "Authorities such as the German DVGW, the British WRAS, the French NF and the Dutch KIWA offer standards and approvals for finished valves, and these are also recognized and accepted by other countries that presently don’t have their own approval regulations. By obtaining and maintaining the most widely accepted water approvals worldwide, we assure our customers that AVK valves always meet the highest quality and safety standards".
The high quality rubber
Germany has its own set of standards for rubber compounds used in drinking water applications, and the same is valid for other European countries as well as for US, China and Australia, among others. Altogether there are at least 20 different sets of standards for rubber compounds worldwide.
Today, AVK is the only valve manufacturer with its own rubber compound manufacturing site. We have developed a family of rubber compounds for drinking water that we consider universal, as it complies with the broadest possible range of approval requirements.
Attention on brass and epoxy material
It is evident that materials like brass and epoxy coating also are of high importance, as these, if not chosen or applied correctly, may also contaminate drinking water. For instance, new EU standards for brass have resulted in a positive list of approved brass materials aiming to set limits for cadmium and lead emission that might migrate into the drinking water. Consequently, AVK has implemented a new brass material for all components, which are in contact with drinking water. Furthermore, only epoxy manufacturers with the main drinking water approvals are selected for AVK valves, and the coating process in our factories strictly follow the application recommendations set by the epoxy manufacturers. In addition, our coating process is GSK approved.
A great investment
All of this adds up to a major investment of time and money for AVK in order to obtain new and maintain existing approvals. "Each approval requires a massive amount of documentation and paperwork, and it can often take weeks or even months to work through the entire approval process" says Niels Jørgen Hedegaard. Re-certification is required every three to five years, and the entire process involves factory audits, product tests and documentation reviews.
The costs are therefore significant. "It’s an expense, no doubt," says Niels Jørgen Hedegaard, "but we regard it as a long-term investment. By testing the quality and safety of our valves against the requirements, we ensure that customers always can rely on AVK valves, as opposed to other valves available in the market that do not meet the strict regulatory standards."
Protection of our drinking water
Drinking water is becoming a scarce resource. Therefore, it is of vital importance that we all do our best not to contaminate it, while distributing it to the users. AVK as a global player within valves is certainly committed to keeping drinking water safe by making the best valves in the water business.
Therefore, investing in AVK valves is a commitment to safe drinking water.